Water
Damage Drying Saves Pentagon $40 Million in Recovery Costs
Munters
Moisture Control Services played a key role in an all out
effort to return the Pentagon to full use after the September
11th terrorist attack that killed more than 125 military and
government workers while ripping a cavernous hole in the side
of the Washington, DC building.
Specialists
in reversing the effects of water damage, Munters used more
than 600 pieces of drying equipment distributing 1.5 million
cubic feet of dry air each minute through more than a mile
of duct work combined in a massive system to dry out the building.
The equipment needed to handle the project was shipped from
many of the company's 30 North American offices. Munters,
the world's largest water damage recovery company, said that
the Pentagon dry out effort was the largest single-building
project in the company's history.
Pentagon
Story Continues Below Photo Essay...
 |
 |
Photo
Essay: |
 |
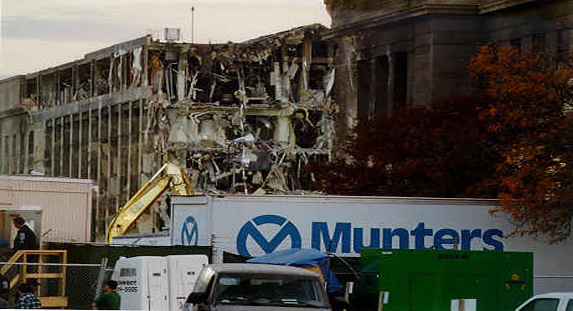 |
Munters
pre shipped equipment so work could begin the same
day it was authorized. |
|
 |
|
|
|
|
The impact
and explosion that occurred when terrorists crashed a hijacked
airliner into the side of the building devastated a significant
area on five floors of the world renowned US military headquarters.
However, water damage--resulting from fire hoses, automatically
activated sprinklers systems, and shattered water lines--
affected nearly 2.5 million square feet of space adjacent
to the crash area that otherwise would have been left intact!
"Millions
of gallons of water flowed throughout the building after the
attack," said Joe Kelley, Munters district manager in the
Washington DC area. In some places water was 18 inches deep
on the floors."
"Munters
dried an area on five levels greater than 33 football fields,
all of which was damaged by the water alone," said Kelley.
Making a conservative estimate, Kelley believes that Munters
will save the Pentagon more than $40 million dollars in reconstruction
expense. "Beyond the money saved, drying allowed this important
space to be back in use months earlier."
Pentagon
managers described the building as composed of five "wedges."
Each wedge has a corner of the building at its center. The
attack occurred between "Wedge 1" and "Wedge 2" with fire
and water damage occurring on both sides of the crash site.
"At the
time of the attack," said Kelley, " Wedge 1 was nearing completion
of a comprehensive, $258 million renovation project. As a
result, much of the space was unoccupied. If the terrorists
had flown into another wedge, or the attack had occurred just
a few weeks later, a much higher number of deaths could have
resulted."
Kelley
says that the Pentagon is constructed as five buildings in,
concentric rings. On the ground level, the exterior buildings
share a common floor. On upper floors they rise as separate
towers. When the airliner hit near ground level, it penetrated
the exterior wall and then slid to the middle of the building.
The devastated area was approximately "v" shaped, with greater
destruction occurring on the outer areas.
"Of course,
the area in "Wedge 1 and 2" that took the direct hit was completely
destroyed," said Kelley. "All that can be done there is to
demolish and rebuild. "Wedge 2" was given a lower priority
by the Pentagon, as it was scheduled to be gutted in a future
renovation and asbestos removal project. But in the "Wedge
1" areas that remain structurally sound to just to the south
of the devastation, a substantial loss was prevented by drying
with our Munters' desiccant dehumidification system.
Munters
offered its services immediately after the disaster. However,
Pentagon building managers could not respond because the FBI
and then the military services had taken command of the building,
giving first priority to national security issues. After security
issues were addressed, Munters was invited by John Kirlin
Construction Company, a subcontractor working with AMEC Construction
on the Pentagon restoration to tour the building and propose
restoration procedures.
"Initially,
we found varying conditions throughout Wedge 1," recalls Kelley.
"But even after extensive water damage, and the delays caused
by the unprecedented security procedures, we felt that Munters
desiccant drying could reduce reconstruction time significantly
and save the majority of these newly remodeled areas."
In areas
furthest from the blast, the "C" zones, Kelley found some
water damage and minor mold development. In "B" zones, water
damage was very heavy and mold growth had become substantial.
In the "A" zones, nearest the crash site, the water damage
was devastating and mold was horrendous. There, mold growth
was well up the walls and in some cases 2 inches thick on
the carpet!
"We proposed
that "C" zones should be addressed without further delay,"
said Kelley. "We knew after a simple walk through that we
could save millions in new construction and prevent mold from
becoming a problem. We could also have the areas dry enough
for use in less than one week."
Kelley
also felt that drying the "B" zone could also provide great
benefit, saving the Pentagon both time and money as it returned
the areas to use, but first priority should be given to "C"
zones.
"By drying
the "B" zones we proposed to save at least 60% of the sheet
rock, virtually all of the new structural and mechanical materials,
as well as eliminate future mold and mildew growth," said
Kelley. "It was to be a salvage operation, but the advantages
weighed heavily in favor of drying over ripping it all out."
"After
our presentation," said Rob Sullivan, Munters Northeast Operations
Manager," we immediately mobilized equipment stationed around
the country. It was no time to pull punches.
The country
was in a crisis. If we got the contract, we wanted no delays."
The next day Pentagon managers authorized Kelley to start
on the "C" and "B" zones located south of the impact in the
newly renovated area.
"Pentagon
officials were most impressed when Munters equipment began
arriving at the Pentagon just hours later," said Sullivan.
"We had electrical generators and Munters dryers at the site
the same day and began assembling our drying system immediately."
"The Munters
team was very effective," said David Rosner, Project Manager
John J. Kirlin, Inc. Their equipment began showing up within
hours. With all they had to do, they never were stressed or
overwhelmed, and it was a big job! They methodically set up
and acted swiftly to new requests and changes. The company
proved very easy to work with!"
The system
had three components: dehumidifiers, air movers and air scrubbers.
The dehumidifiers were hoisted onto the damaged floors through
bomb resistant windows specially removed to expedite the process.
Once on the floors, the dehumidifiers drew in humid outside
air, dried it to an extremely dry condition, and pumped the
air into the damaged areas. Air movers and network of flexible
duct distributed the air to all parts of the "C" and "B" areas.
Simultaneously, the air scrubbers filtered the air for dust
and mold spores kicked up by restoration activities.
Initially,
Kelley expected only to work in the "C "and "B" zones, but
several days into the project, things changed.
"When
we were awarded the "C" and "B" phases of the project, it
seemed unlikely that we would get the opportunity to dry "A"
zones. A decision had been made to put front loaders on each
floor and bulldoze everything inside. Mold growth was so advanced
we had to wear respirators to go in and look around."
However,
pleased with the substantial progress being made in the "C"
and "B" zones, officials modified their plans and awarded
Munters the "A" zones to dry, as well.
"After
appropriate measures were taken to deal with the environment
in the "A", Zone, we were asked to begin the drying process.
As a result, the Pentagon will save millions of dollars in
new structural materials, plus electrical and mechanical equipment
throughout the "A" zones," said Kelley.
|